the stamp charging |
|
|
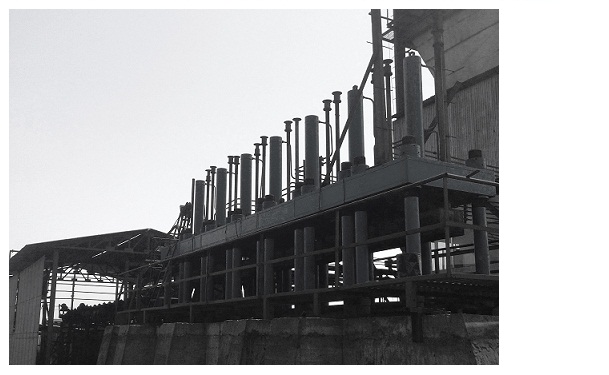 |
Carbon Edge entered a new phase in coke making in February 2015. In the existing unit we installed the first stamp charging machine based on hydraulic press for any by-product coke manufacturer in the country. We are committed to serve our customers to the fullest and it is always our endeavor to provide consistent quality coke of the highest standards to all our customers.
We are constantly innovating and carrying out R&D to help make coke for our consumers that can match the best quality coke in the world. We are aware that coke causes up to 50% of the costs during the pig iron production. The availability of high quality coke is thus of prime importance for the competitive ability of the iron producing industry and serving our clients is our primary objective and duty.
During the stamp charging process the coal is stamped outside the coke oven, into a single "briquette" (coal cake), having almost the same dimensions as the oven chamber. This coal cake reaches a density of up to 1.15 T/m3 (on wet coal basis with 10-12% moisture)-about 30% more than with the loose coal-charge during conventional top charging systems. Whereas for top charged coke this value is around 0.8 t/m3 or less. The coal cake is then charged into the oven from the pusher side rather than top charge. Additional changes are required to be made in the average grain size of coal charge through stamping to provide cake stability and improve coke quality. |
Carbon Edge is always ahead of its competitors as far as adopting technology is concerned. There is a great possibility that pollution control department will make stamp charging compulsory for all coke manufacturers in India in few years to reduce pollution and ensure coke manufacturers adopt more green technologies for coke making. We are trying to walk a few steps ahead to ensure that we are well prepared when such rules and regulations come into place.
The major benefits of stamp charging coke which we have observed are the following:
- Coke Quality has improved remarkably with CSR around 70 and CRI below 22.
- Both M10 is below 7 and M40 above 88.
- Improvement of yield of Blast Furnace Sized Coke.
- Improvement of Blast Furnace Productivity.
- Reduction in wastage of coal charge by 2%
- Improvement in coke yield.
- Improvement in porosity of coke.
|